|
Post by Voltan on Jun 25, 2014 18:22:58 GMT
That came out really good Bryan.
|
|
|
Post by L Driggers (fallen) on Jun 25, 2014 21:50:50 GMT
Maybe I should just have you do the hilt, grip and pommel work on the future gladius I'm planning to do nest after I finish a couple of customers swords.
|
|
|
Post by LG Martial Arts on Jun 25, 2014 22:11:03 GMT
That's a fantastic job you did... final product is inspiring me to buy a H/T blade blank and make myself a custom sword. BTW, have you considered using MAP gas instead of propane? The rigging is almost the same price wise, except the torch is a little bigger/more stout since MAP burns a lot hotter than propane.
|
|
|
Post by chrisperoni on Jun 26, 2014 1:29:52 GMT
This is freaking wicked stuff! +2
|
|
|
Post by Lonely Wolf Forge on Jun 26, 2014 4:38:55 GMT
you may have mentioned it, but mind sharing where you got the steel doughnut for the pommel? ive been looking for steel O bars for a long time but all i can find are extremely thin ones
|
|
|
Post by aussie-rabbit on Jun 26, 2014 9:49:58 GMT
Have you looked for pressure pipe at your nearest steel merchant - an alternative is a length of hydraulic ram - more info here www.practicalmachinist.com/vb/ge ... el-143628/
|
|
|
Post by Bryan Heff on Jun 26, 2014 11:03:55 GMT
www.speedymetals.com/c-8242-round-tube.aspxThey will cut either bar stock, round etc...and in this case round tube to your specific length as long as its 1/4" or bigger. So I order a piece that was 5/8" thick (actually forget my exact width now, but you get the idea).
|
|
|
Post by Lonely Wolf Forge on Jun 26, 2014 17:46:20 GMT
thanks! i had looked allover that site and couldnt find it but your link took me straight to what i needed! cheers
|
|
|
Post by L Driggers (fallen) on Jun 26, 2014 19:00:10 GMT
Agian McMaster-Carr.com they have heavy wall tubing.
|
|
|
Post by brotherbanzai on Jun 26, 2014 21:47:19 GMT
Nice work Bryan Heff, I've done a couple similar spiral grip wraps and the fitment can be a real pain. I would agree with you that it might look better to cut down the leather at the pommel end, larger pommel ring might have been nice as well.
Hey Findlithui, clamp the tang in a bench vise when hot peening a pommel. It will act as a heat sink and help prevent the blade from losing it's temper from the heat you're putting into the end of the tang. Also, you can heat the end of the tang up before putting the pommel on so less heat is transferred into the pommel. Then slide on the pommel (tap it on with a hunk of wood if the tang has expanded too much to slide all the way on) and peen. Usually have to heat it some more after the initial heating anyway, but that will help. An oxy/acetylene torch would be much faster than a propane torch if available.
|
|
|
Post by Bryan Heff on Jun 26, 2014 22:50:19 GMT
Thanks all for the words. Thanks BB for the advice about clamping the tang in the vice too, never thought of that. I went back and forth on the diameter size of the pommel...had a 2" version as well I'm mind but the thin width of the h/t blade, I went with a 1 3/4" pommel which is still a bit wider than the blade is wide...but I hear what you are saying. I may do another one up with a bigger pommel on the fullered h/t blade... For basically a 100 buck blade...it's really hard to beat the value there. Plus I still want a go at a more interesting cross guard type with spatulate ends....next project perhaps.
|
|
|
Post by Lonely Wolf Forge on Jun 26, 2014 23:03:03 GMT
i bought the one that was a size up from 1 1/2" with 1/4" walls. its going on a dagger im currently finishing up
|
|
|
Post by Bryan Heff on Jun 27, 2014 18:42:41 GMT
I did a different grip treatment....I like this MUCH better. I also trimmed off what amounted to extra leather down around the pommel. 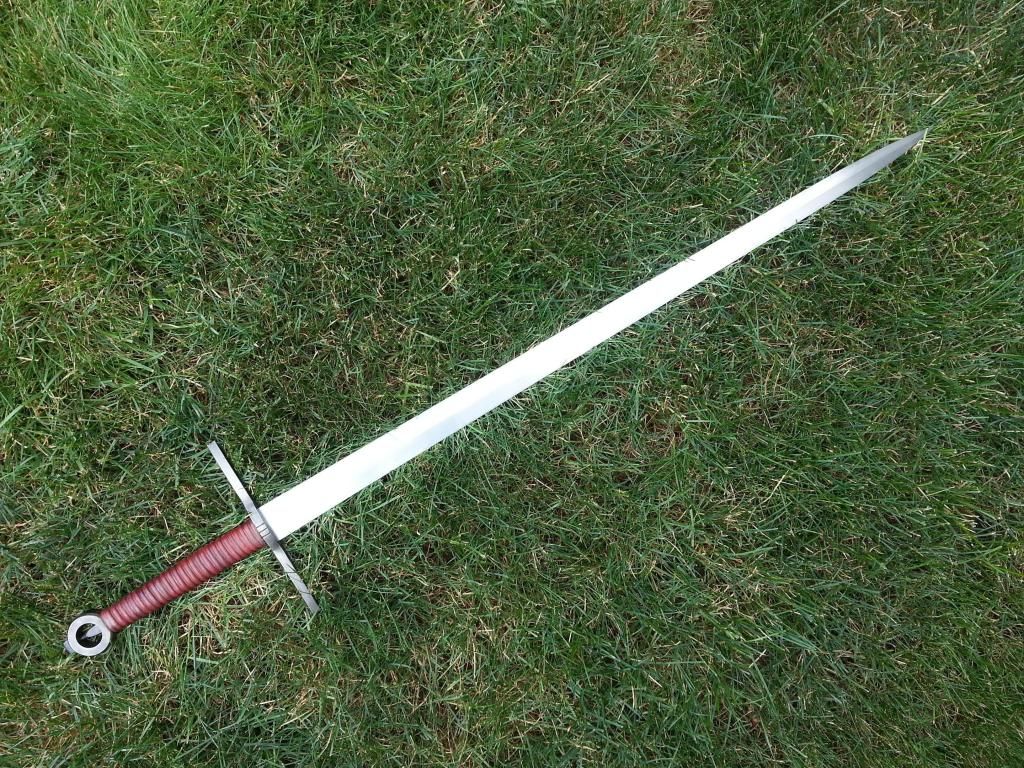 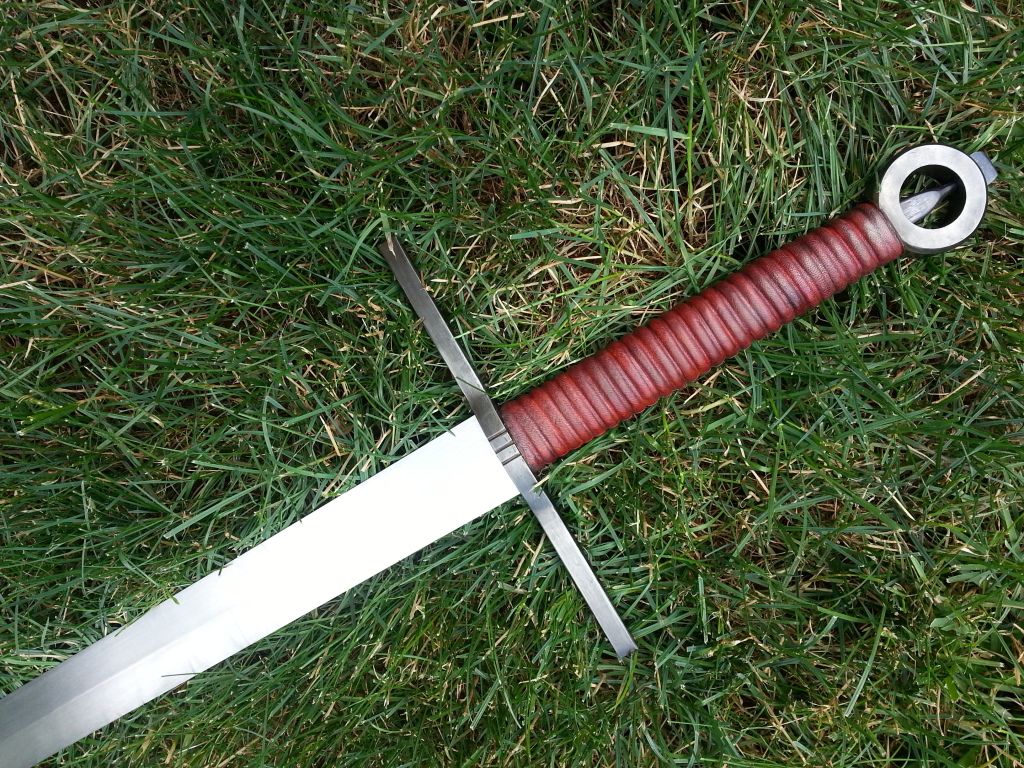
|
|
|
Post by Lukas MG (chenessfan) on Jun 27, 2014 18:53:17 GMT
MUCH better Looks great.
|
|
|
Post by Voltan on Jun 27, 2014 22:23:10 GMT
Awesome, Bryan!
|
|
|
Post by aussie-rabbit on Jun 28, 2014 3:44:24 GMT
Love the colour too
|
|
|
Post by brotherbanzai on Jul 1, 2014 13:53:47 GMT
Yep, much better. Nice job.
|
|
|
Post by dustinf11 on Jul 28, 2015 4:16:45 GMT
This looks really great. Working with metal by just straight stock removal is hard work. But that's all I know how to do, and not nearly as nice as this.
|
|
|
Post by StevenJ on Jul 29, 2015 0:00:47 GMT
It is very good I must say. I never made fittings myself but have considered it before.
|
|
|
Post by Derzis on Jul 31, 2015 0:36:37 GMT
Very nice! I like your choices for that sword. Simple but elegant.
|
|